Бізнес
Економіка
70 000 оттенков Maserati: как не вылететь в трубу при производстве дорогих прототипов
Требование индивидуализированного массового производства бросает вызов обрабатывающей промышленности всего мира. Производство будущего предусматривает диджитализацию всех процессов.
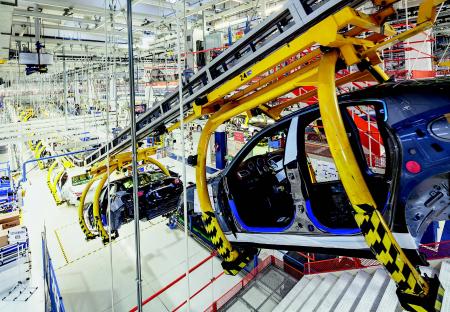
Более века назад Генри Форд дал толчок промышленной революции: в 1913 году он запустил свой первый конвейер, создав тем самым основу для современного массового производства. Позднее инженеры и ученые на базе новейших технологий автоматизации усовершенствовали этот принцип, что дало возможность производить миллионы или даже миллиарды изделий неизменно высокого качества. Но потребности клиентов и технические возможности продолжают эволюционировать. Следовательно, растут и требования к компаниям-производителям, ведь сегодня клиенты могут напрямую сообщать производителю, что именно и когда они хотели бы приобрести. Ответом компаний на подобные вызовы должен стать более быстрый вывод продукции на рынок, максимальная гибкость и индивидуализация массового производства.
Комплексный подход
За счет дальнейшей оптимизации автоматизированного производства таких амбициозных целей не достичь. Необходим комплексный подход. Это понимают многие компании и научно-исследовательские организации, которые интенсивно работают над технологиями производства будущего. Прежде всего, это предусматривает диджитализацию всех процессов.
На цифровом заводе будущего весь задействованный персонал, начиная с разработчиков и проектировщиков и заканчивая сотрудниками маркетинговых и сервисных подразделений, должен получать доступ к единым данным – причем такой же доступ к данным должны иметь коллеги на других производственных площадках, а также с внешние специалисты, поставщики и даже с конкуренты в рамках все более широкого обмена информацией.
Основой для этого служат комплексные решения по управлению жизненным циклом продукта (PLM), например, программный комплекс NX от Siemens для разработки и производства изделий или наиболее популярная в мире PLM-система Teamcenter.
Опыт Maserati: семьдесят тысяч индивидуальных комбинаций
При разработке этой легендарной марки спортивных автомобилей производитель Fiat Chrysler Automobiles (FCA) сделал первые шаги в направлении индивидуализированного массового производства. Одна из целей Промышленности 4.0 заключается в удовлетворении самых разнообразных пожеланий клиента, вплоть до экономически оправданного производства единичной продукции. Уже сегодня новая модель Ghibli доступна в различных вариантах исполнения. "Всего возможно 70 тысяч индивидуальных комбинаций", – подсчитывает менеджер FCA Анна Адиларди из подразделения информационных-коммуникационных технологий.
Производить эффективно, гибко, индивидуально, доступно по цене и качественно – с этой задачей сталкиваются все производители автомобилей высокого класса. Кроме того, они вынуждены постоянно сокращать время вывода на рынок новых моделей, а также из-за снижения глубины производства управлять растущей сетью поставщиков. Справиться с этими вызовами можно только при условии сплошной диджитализации всех процессов в автомобилестроении вплоть до каждой функции и на каждом уровне.
Еще одним инструментом эффективного производства является цифровой двойник (Digital Twin), которого можно создать с помощью программного решения PLM от Siemens. Такой двойник сыграл ключевую роль при разработке Maserati Ghibli: параллельно с физической разработкой автомобиля на основе цифровых копий создавался с точностью до последнего винтика ее виртуальный образ. В ходе последовательной оптимизации параллельно использовались данные реальной и виртуальной моделей, что позволило кардинально сократить материальные и временные затраты на разработку автомобиля. Цифровой двойник может также значительно снизить затраты на тестирование. Процесс так называемого реверс-инжиниринга предусматривает тестирование прототипов или уже изготовленных серийных машин на дорогах или испытательных треках для сбора данных. Цифровой двойник позволит воспроизводить на экране компьютера тестовые испытания при различных условиях сколь угодно часто и виртуально оптимизировать новые автомобили. "Программное обеспечение Siemens помогает нам существенно сократить количество дорогостоящих прототипов", - считает менеджер Maserati Жан Лука Антинори. Преимущества PLM-решений от Siemens сегодня используют около 90% всех автопроизводителей в мире.
В компании «Сименс Украина» также уверены, что будущее промышленности лежит именно в создании цифрового пространства для инжиниринга и тестирования продукта. Начальник отдела маркетинга департамента «Автоматизация промышленности, непрерывные процессы и приводы» Марина Парфинская комментирует: «Создание цифрового двойника не только помогает в сокращении затрат на создание прототипов, но и сокращает время “time-to-market” – от создания идеи модели до её воплощения в серийном производстве. Это позволяет компании существенно ускорить возврат средств, инвестированных в новинку».
Стоит отметить, что некоторые предприятия украинской промышленности уже пришли к созданию новых моделей и планированию производства с помощью цифрового пространства. Однако в целом украинская промышленность все ещё в самом начале этого пути.
Благодарим за предоставленные материалы ДП «Сименс Украина».
Оценка материала:
70 000 оттенков Maserati: как не вылететь в трубу при производстве дорогих прототипов27.10.2015